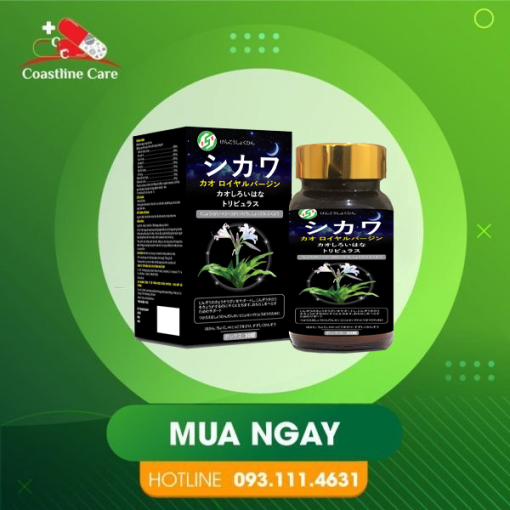
Controlar la calidad de un producto o un servicio. Se puede analizar qué factores generan problemas de calidad en la elaboración de un producto o un servicio para solucionarlos.
There can be a threat of concentrating way too intensely on personal components as opposed to taking into consideration how they may interact with one another.
Involve a various team: Ishikawa Diagrams function greatest when used in a bunch setting. To make sure a nicely-rounded standpoint, try out to incorporate a diverse team of folks from several departments or regions of experience.
[ Touch-roll kind Thickness Measurement Program ] Substantial accuracy eddy existing, contact-roll style thickness measurement procedure. Usage of eddy recent technique makes the system outstanding to some other measurement techniques as it can offer highly exact measurements of thickness of polymer movies and rubber sheets constantly with no remaining affected by ambient environment with h2o, oil or dust etcetera. Speedy RIVERNEW
” which mistakenly presumes that complications and signs and symptoms are mutually exceptional categories. A problem is really a problem that bears advancement; a symptom is definitely the impact of a bring about: a problem is usually both equally a difficulty as well as a symptom.
Making an Ishikawa Diagram is a straightforward procedure that begins with identifying the problem and breaking it down into its component parts. Here’s a step-by-move tutorial for making an Ishikawa Diagram:
That can help framework the technique, the classes are frequently picked from among the frequent types shown below, but could emerge as something special to the applying in a specific situation.
Using nha thuoc tay this, the clinic can begin to Focus on minimizing the chance of infection via, for instance, an infection Regulate teaching, alterations to cleaning protocols or improved interaction in just teams.
Will need aid planning your excursion to Japan? My identify is Robert Schrader, and i am a nha thuoc tay Japan vacation expert with virtually ten years of knowledge below my belt.
You can utilize paper checklists or spreadsheets to outline the issues or use precise applications like SafetyCulture (formerly iAuditor) to capture and Arrange your specified difficulties.
Combining the Ishikawa diagram’s Visible composition With all the 5 Whys methodology is possible. In this approach, the potential results in of a challenge are 1st mapped while in the Ishikawa diagram.
This is when the Ishikawa Diagram comes into Perform—a visible Resource that facilitates the analysis of possible brings about of a challenge.
An Ishikawa (or fishbone) diagram needs to be designed after the situation assertion is prepared and facts has actually been gathered. An Ishikawa diagram must be seen like a graphical depiction of hypotheses that might make clear the failure beneath investigation.
The lights may be a contributing result in, nevertheless it nha thuoc tay should not be the very first 1 investigated. The Ishikawa diagram should be expanded every time five Whys is applied. One example is, the department could wind up as material → part not mounted → personnel skipped operation → work environment much too darkish → inadequate lighting → light-weight bulbs burned out.